Automation and robotics are rapidly reshaping the manufacturing landscape, and Pittsburgh initiatives are stepping up to support smaller manufacturers in their pursuit of innovation.
A local research institute is helping small and medium-sized manufacturers in Southwestern Pennsylvania (SWPA) ride the wave of the future, hoping it’ll prevent them from being left behind.
The Advanced Robotics for Manufacturing (ARM) Institute, an innovation center in Pittsburgh’s Hazelwood neighborhood, is now accepting applications for its Robotics Manufacturing Hub program. The program helps manufacturers evaluate, prototype and test robotics efforts for free, as a part of the $62.7 million New Economy Collaborative efforts to build up SWPA.
“The number of workers available in the US is starting to dwindle, so the ability to use technology to improve quality and boost production is going to be vital moving forward,” Tasha Miller, ARM’s senior program manager, told Technical.ly.
Manufacturers who join the cohort aren’t required to adopt robotics. Rather, the no-cost resource aims to help them evaluate whether robotics makes sense for a particular manufacturing process, according to ARM COO Jay Douglass, in a recent news release.
“We aren’t selling services,” Douglass said, “but instead acting as a neutral subject matter expert to ensure that manufacturers who do decide to invest in robotics receive the highest possible return after purchasing a robot.”
The deadline to apply for the program is Nov. 22.
The NEC, funded by the federal Build Back Better Regional Challenge grant, is an 11-county coalition of over 90 local organizations. The organization is leveraging federal aid, including the $14.5 million it gave to the ARM Institute, to fund projects that enhance the region’s leadership in robotics and autonomy.
Small companies can lose more by taking a leap of faith on tech
Adopting automation and robotics can be a big investment and a much larger risk for smaller manufacturers to pursue, especially if they’re uncertain about the technology. Unlike larger manufacturers, these companies can’t always absorb a loss if their investment doesn’t pan out.
The program’s efforts to de-risk these investments aim to help manufacturers better recoup the cost of implementing robotic systems and troubleshoot problems along the way, Miller said. She estimates successful robotic systems can yield anywhere from a one to five-year return on investment. This can be from quality improvements that reduce rework, savings on labor costs or a 20% to 50% increase in output.
“Some people are able to run a robot overnight if it’s set up correctly,” Miller said, “so there’s more than just a trade of a human hour for a robot hour.”
Penna Flame, a third-generation, family-owned and operated flame hardening manufacturer in Beaver County already had a robot when it participated in the program’s previous cohort. However, employees were still manually lifting and packing cast parts that weighed 30 pounds or more because the manufacturer’s robot needed further customization to undertake packing tasks.
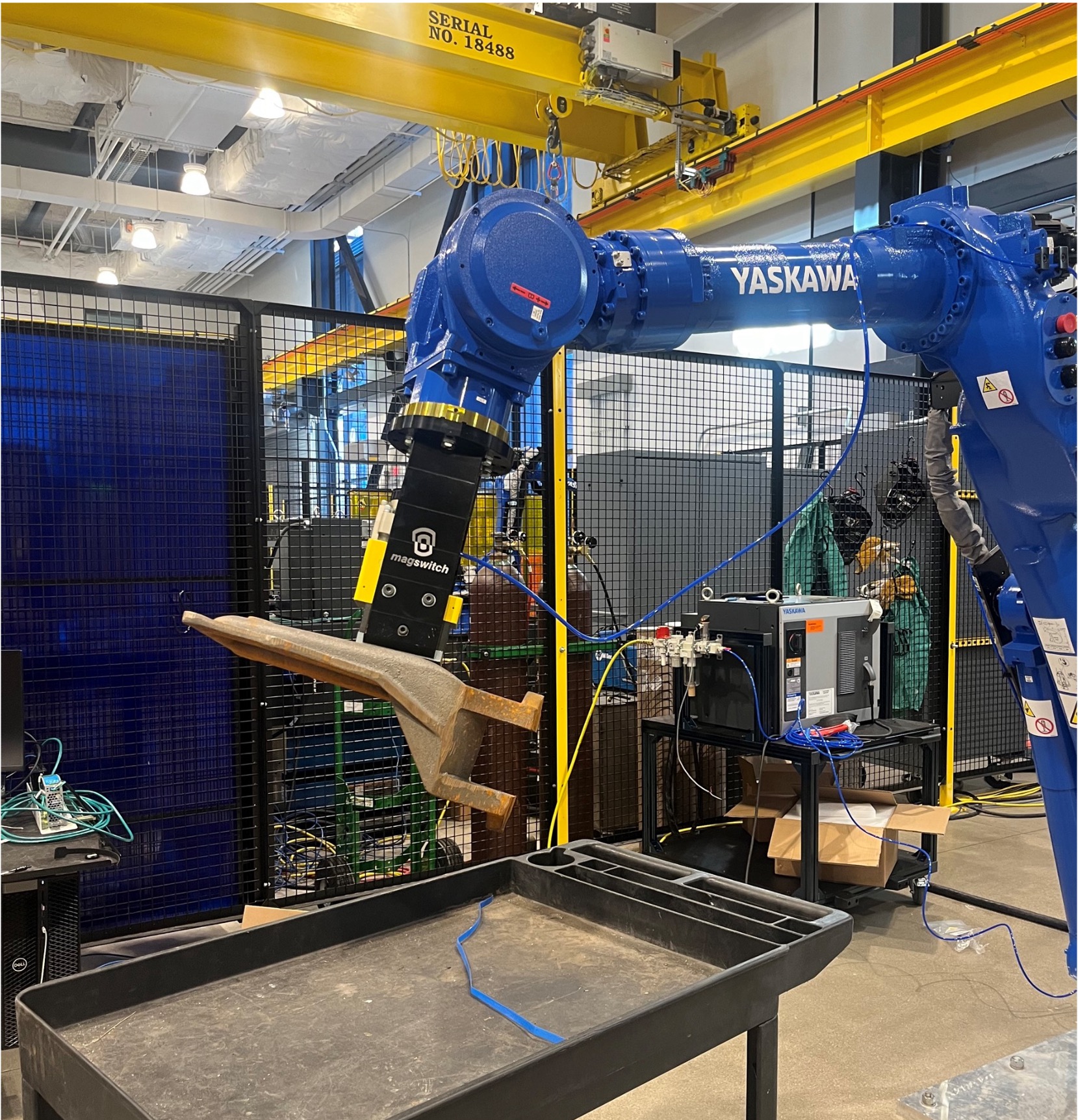
After an engineering analysis and testing of the robotic system, the Robotics Manufacturing Hub Team provided Penna Flame with a proof-of-concept for an improved system, which the manufacturer is currently working to install.
“It’s been incredible to see how rapidly went from not knowing if this was ever going to work to having them produce a proof-of-concept and a real, solid plan,” said Penna Flame Vice President Andrew Orr.
The program has positively impacted 15 smaller manufacturing companies across Southwestern Pennsylvania since launching in April 2023, according to Miller’s estimates.
Workers also need training on how to adapt to the new jobs
When smaller manufacturers consider automation, one of the most important questions they must ask is whether their workforce is ready for the transition, Miller said.
The adoption of robotics systems can benefit manufacturers, but workers don’t always benefit equally.
The introduction of industrial robotics between 1990 and 2014 resulted in a decrease of 420,000 to 720,000 jobs in the US manufacturing industry, according to a 2020 study in the University of Chicago Press Journal of Political Economy. The study also found evidence of a decline in wages among those who did not lose their jobs.
Automation may also have a negative mental toll on workers, according to subsequent research from think tank the Brookings Institution. Manufacturing employees can suffer from stress associated with adapting to new technology and increased anxiety over job displacement.
“There can be a little bit of a clash between people and technology out on the manufacturing floor,” Miller said. “In those scenarios, we’ve been able to come up with ‘Get Well Plans’ to try to bring the robots back in and walk them through the process.”
ARM connects manufacturers with workforce training through partner programs and other NEC initiatives. While the process can be difficult in some ways, operating robots is becoming increasingly easier, according to Miller.
Instead of trying to decipher lines of code to operate a new system, it’s more like using a smartphone nowadays, she said.
“I encourage [manufacturers], even if they’re just curious and not even seriously thinking of pursuing automation, to get that familiarization and have it in the back of their minds,” Miller said. “Then maybe start asking questions … to get on the road to adopting robotics.”